白金会员
已认证
在粉体加工领域,精准配料与高效混合是提升产品质量和生产效率的核心环节。苏州天启粉体设备有限公司凭借其深耕粉体工程15年的经验,推出了一套集自动化、智能化与模块化于一体的粉体集中自动配料设备。该系统通过整合高速混合、精准计量、智能控制等关键技术,广泛应用于锂电、化工、医药、食品等行业,解决了传统工艺中精度低、能耗高、粉尘污染等问题。本文将从系统架构、核心技术、应用场景及创新优势等方面展开分析。
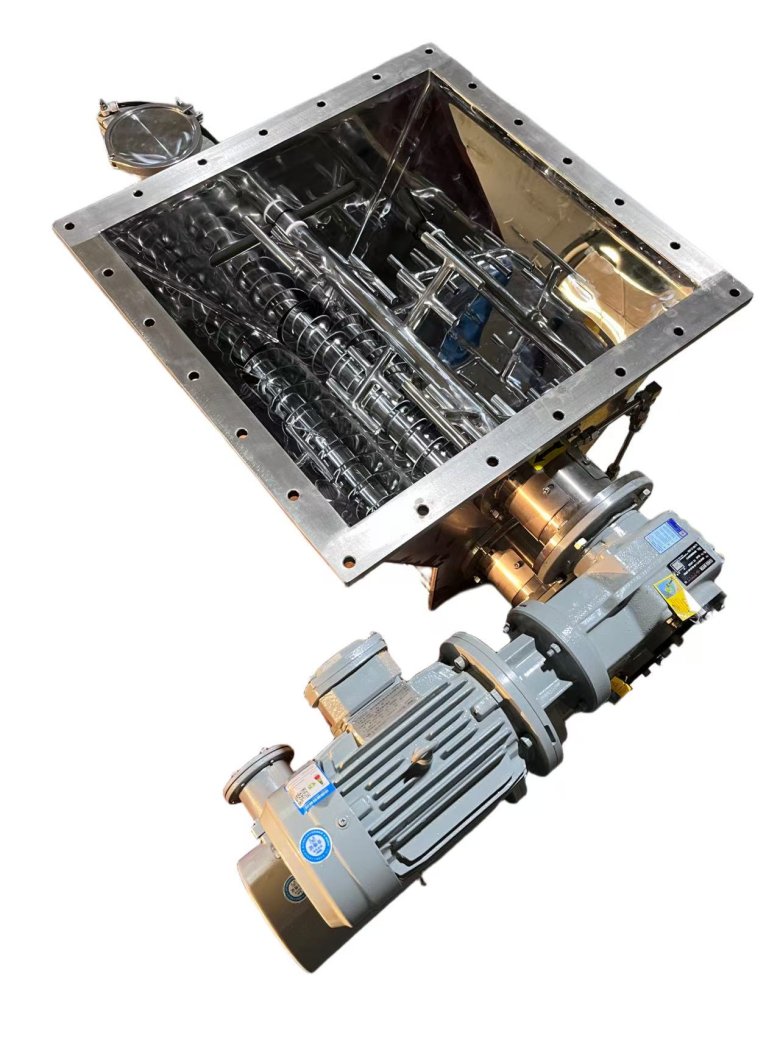
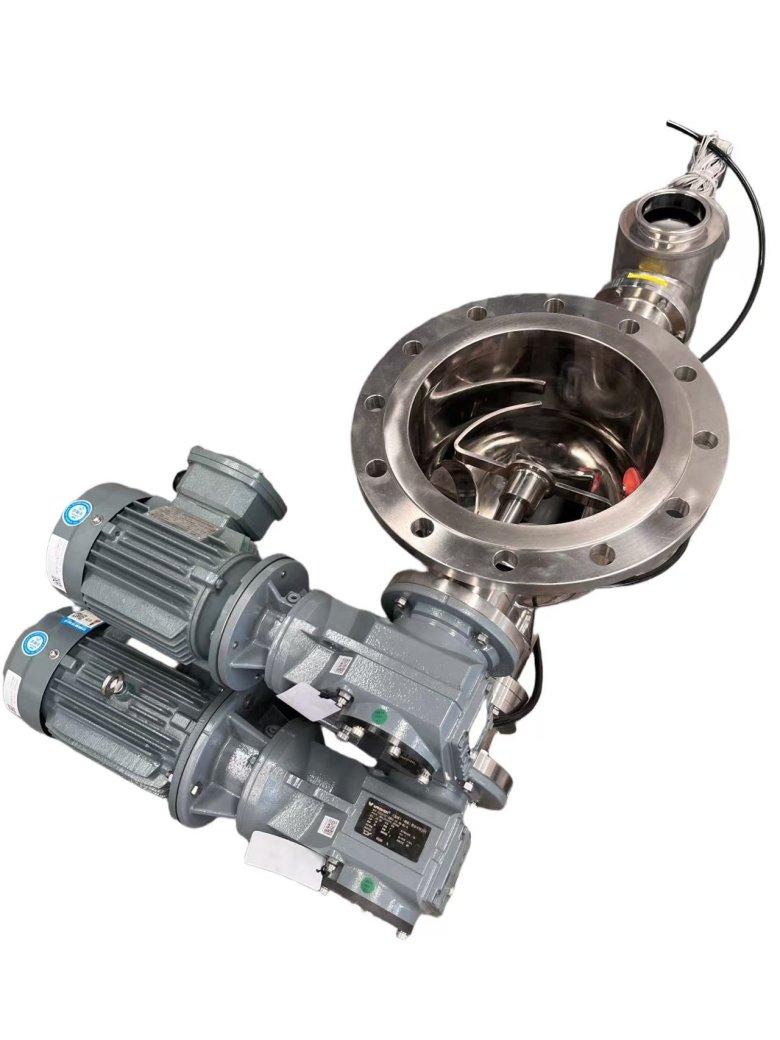
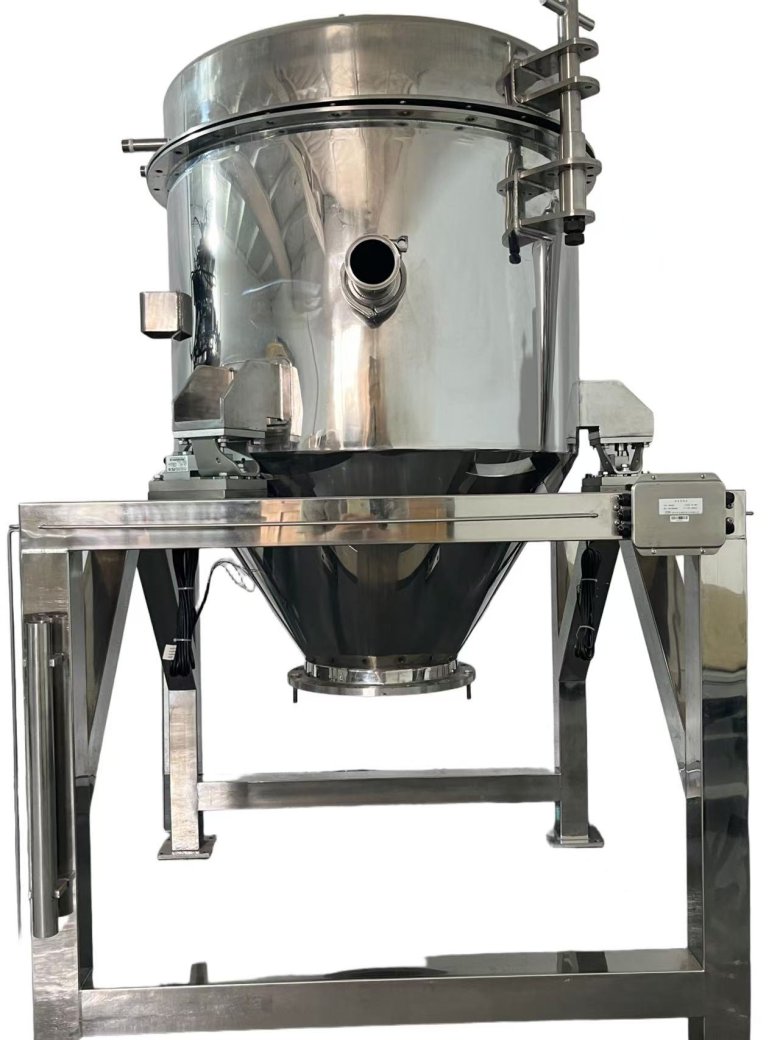
一、系统架构与核心组件
苏州天启粉体集中自动配料系统采用分层模块化设计,涵盖物料存储、输送、混合、计量及控制五大功能模块,形成全流程自动化闭环。其核心组件包括:
高速混合设备
HM系列高速混合机:搭载涡轮桨叶设计,最高转速达3000rpm,支持粉体与液体、粉体与粉体的高效混合,尤其适用于锂电池正负极材料的均匀分散。
螺带混合机:通过S型搅拌桨强制循环物料,避免结块,混合效率提升40%,适用于大规模预混合场景。
精准计量与输送系统
螺旋输送机:包括双向U型螺旋、带破拱子母螺旋等型号,输送能力覆盖5-50吨/小时,支持正负压输送(耐受0.3MP压力),解决传统螺旋易堵料问题。
失重式计量称:结合PLC控制,实现动态配料,精度误差≤0.2%,满足医药、食品行业高精度需求。
环保与安全设计
全密封输送管道:结合高效除尘设备,粉尘排放减少40%,符合环保法规要求。
设备状态监测模块:通过传感器实时监控轴承温度、振动等参数,预测性维护降低故障率。
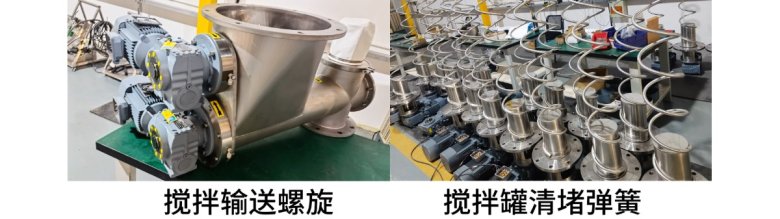
二、技术创新与优势
动态配比与智能调控
系统集成算法,根据物料特性(如粒径、溶胀性)自动调整混合时间、转速及流量,实现“一料一策”。例如,在锂电池材料混合中,通过PID调节变频电机转速,确保正负极材料的均匀性。
模块化与定制化设计
支持非标定制,如钛材材质升级、输送角度调整等,适配高腐蚀性或特殊工况需求。例如,针对氢氧化锂粉末输送,采用带破拱子母螺旋设计,解决流动性差的问题。
低能耗与绿色制造
混合机功率优化,结合“无尘化+低能耗”方案,单位能耗降低20%,响应中国“双碳”政策。
高兼容性与扩展性
可无缝对接MES系统,实现生产数据实时采集与追溯,支持多配方快速切换,满足制药行业频繁换料需求。
三、典型应用场景
锂电材料制备:对正负极材料(如高镍三元、硅碳复合材料)进行预混合与分散,批次一致性达99.5%,助力新能源电池性能提升。
医药原料混合:实现活性成分与辅料的无尘混合,精度误差≤0.1%,符合FDA与欧盟GMP标准。
食品加工:在奶粉、调味料生产中,动态配比系统确保每批次口感一致,同时CIP清洗减少交叉污染风险。
化工催化剂制备:高速混合机与螺旋输送机联动,实现催化剂颗粒的均匀分散,提升反应效率。
四、行业影响与未来趋势
苏州天启的粉体集中自动配料设备通过智能化与模块化设计,推动粉体加工行业向高效、精准、绿色方向转型。根据Mordor Intelligence预测,全球粉体处理自动化市场2025年将突破50亿美元,中国占比超40%。未来,随着工业4.0技术的深化,粉体行业必将进一步融合数字孪生、5G远程运维等技术,实现“无人化+预测性生产”,为高端制造提供更强支撑。苏州天启粉体粉体设备也必将以技术创新为核心,着力解决了传统工艺的痛点,推动重新定义粉体加工的智能化标准。深耕在锂电、医药等领域的成功应用,努力成为全球粉体行业升级的重要推动力。
